Concrete pump trailer is a machine that uses horizontal or vertical pipes to continuously transport concrete to the pouring point. It can transport concrete horizontally and vertically at the same time and works reliably. Concrete pumps are suitable for situations where the amount of concrete is large, the operation cycle is long, and the pumping distance and height are large. It is one of the important equipment in the construction of high-rise buildings.
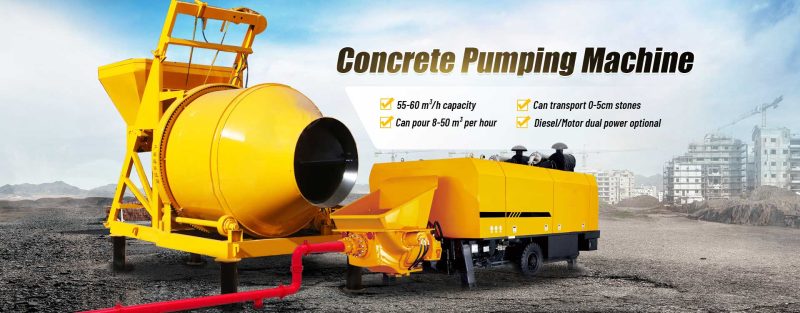
Types of Concrete Pump
Concrete pumps are divided into three types according to the structure of the distribution valve: tubular valve, gate valve and rotary valve. Currently commonly used are hydraulic concrete pumps with double-cylinder piston tubular valves and gate valves. This section focuses on these two types of concrete pumps.
According to the displacement size
They can be divided into small (pump displacement less than 30 m3/h), medium-sized (pump displacement 30-80 m3/h) and large concrete pumps (pump displacement greater than 80 m3/h).
According to the driving form
The concrete pump can be divided into electric and internal combustion diesel concrete pumps.
According to the mode of movement
It is divided into fixed, trailer and self-propelled concrete pumps (concrete pump trucks). Stationary concrete pumps are mostly driven by electric motors and are suitable for construction sites with large quantities of work and little movement. The trailer-mounted concrete pump is a pump mounted on a simple trolley. Because it is equipped with wheels, it can be easily moved at the construction site and towed and hauled on the road. This form is more commonly used in our country.
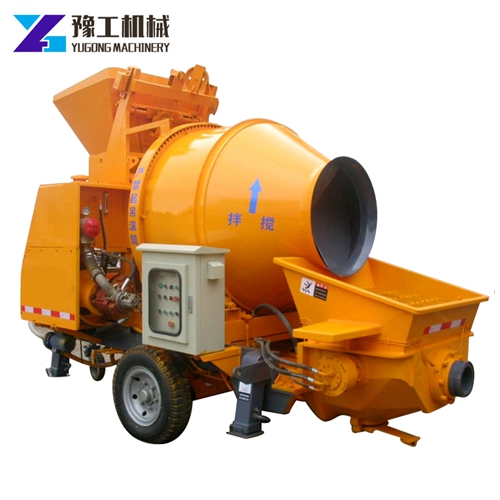
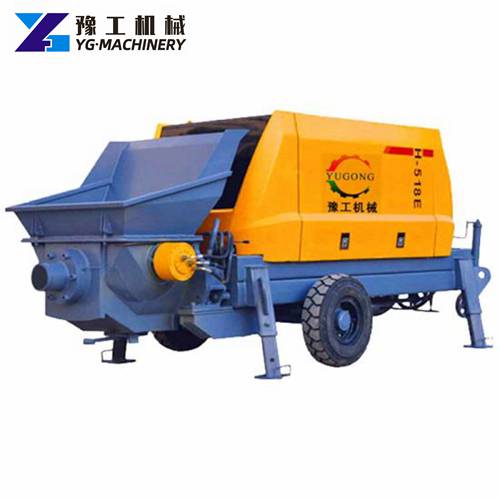
Structure and working principle of concrete pump
The HBT60 trailer-mounted concrete delivery pump is a hydraulic double-cylinder piston concrete pump driven by a diesel engine. The pumping system adopts a closed oil circuit, constant power control, and has the functions of hydraulic stepless speed regulation and concrete delivery volume. The pump is mainly composed of a power unit, a concrete pushing mechanism, a concrete distribution valve, a concrete mixing mechanism, a hydraulic system, an electronic control system, a lubrication system and a supporting traveling mechanism.
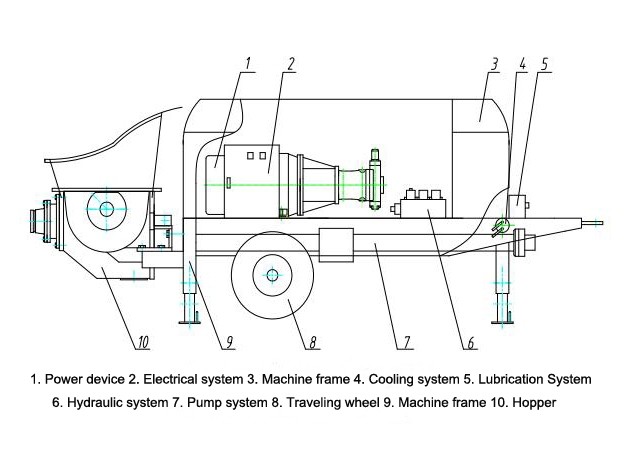
1) Power device
The concrete drag pump power device has two types: diesel engine and electric motor. It consists of diesel engine (or electric motor) 1, coupling 2, pump base 3, main pump 4 and gear pump 5. The engine (motor) power and the selection of the main oil pump must match. The main oil pump adopts an axial piston variable pump. The output flow is proportional to the driving speed and the displacement of the pump, and can vary steplessly between maximum and zero, with Constant power control, pressure cut-off and electrical proportional flow adjustment functions.
2) Pumping mechanism
The pumping system is a power actuator that converts hydraulic energy into mechanical energy. Its function is to push the concrete to overcome the resistance of the pipeline and reach the pouring site.
3) Concrete distribution valve
The function of the distribution valve is to control the concrete flow path in the hopper, two concrete cylinders and delivery pipes. The distribution valve is a key component of the piston concrete pump. The main difference in the structure of the concrete pump is the distribution valve. It directly affects the structural form, suction performance, pressure loss and application scope of the concrete pump. Such as the layout of the hopper and mixing device, the outlet form of the pump, the transport volume efficiency, and the reliability of the work, etc.; 90% of clogging failures in pumping concrete occur at the distribution valve.
The two cylinders of the concrete pump share a collecting hopper, and the two cylinders are in the suction stroke and discharge stroke respectively. The working cylinder in the suction stroke is connected with the hopper. The working cylinder in the discharge stroke is connected to the delivery pipe, so the distribution valve should have the function of two-position four-way (through the hopper, two cylinders and delivery pipe).
Distribution valves can be divided into three categories: rotary valves, gate valves and tubular valves. Currently, the distribution valves commonly used in hydraulic concrete pumps are gate valves and pipe valves.
4) Hopper and mixing system
The volume of the hopper should be adapted to the concrete delivery capacity of the pump. The upper part of the hopper is equipped with a grid screen to prevent large pieces of aggregate or debris from entering the hopper. There are mixing blades in the hopper, which perform secondary mixing of the concrete mixture and have the feeding function of pushing the concrete mixture to the concrete distribution valve port.
5) Pump support and traveling mechanism
The support and traveling mechanism are mainly composed of chassis, axle (including running wheels), guide wheels and outriggers.
The chassis is the basic component for connecting the various parts of the drag pump. It is welded by profiles and steel plates and plays a supporting role in supporting each component. The front of the chassis is connected to the hopper, and there is a trailer at the rear, which can transport the trailer pump from one construction site to another.
6) Water pump device
The water pump device is a water washing device that uses a gate valve drag pump to clean pipes and pumps. It consists of water tank, water filter, water pressure gauge, oil tank, water valve four-way block, discharge valve, suction valve, etc.
7) Cooling system
There are three cooling methods for hydraulic oil: water cooling, air cooling, and air cooling + water cooling. Different cooling methods can be selected according to regional climate differences and construction conditions.
Why the concrete pump is important in Modern Construction Industry?
Concrete pumps are essential pieces of equipment in the modern construction industry. They allow contractors to place concrete quickly and efficiently, even in hard-to-reach locations.
- Increase efficiency: Concrete pumps can place concrete much faster than manual methods, such as wheelbarrows or concrete buggies. This can save contractors a significant amount of time and labor costs, especially on large projects.
- Improve quality: Concrete pumps can help to improve the quality of concrete pours by reducing segregation and entrapped air. This is because concrete is pumped under pressure, which helps to ensure that it is evenly distributed and compacted.
- Reduce labor costs: Concrete pumps require fewer workers to operate than manual methods. This can save contractors money on labor costs, and it can also help to improve safety on the job site.
- Increase versatility: We can use concrete pumps to place concrete in a variety of locations, including high-rise buildings, bridges, and tunnels. They can also be used to place concrete in hard-to-reach areas, such as behind walls or under slabs.
- Reduce the environmental impact of construction: Reduce noise pollution and dust emissions. They can also help to conserve fuel and reduce greenhouse gas emissions.
- Improve job safety: Concrete pumps can help to improve job safety by reducing the risk of injuries to workers. This is because workers do not have to manually lift or carry heavy buckets of concrete.
In conlusion
Overall, concrete pumps are a vital part of the modern construction industry. They are essential tools for contractors who want to improve the efficiency, quality, and safety of their concrete pours. They help contractors to build stronger, more durable, and more sustainable structures.