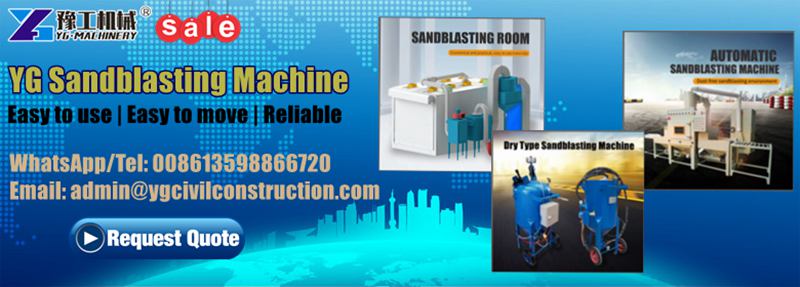
In this blog, we will talk about the types of sandblasters, how the sandblasting machines work, and the difference.
What is a sandblasting machine?
The sand blasting machine is the impact and cutting action of the abrasive on the surface of the workpiece, so that the surface of the workpiece can obtain a certain degree of cleanliness and different roughness, so that the mechanical properties of the surface of the workpiece can be improved, thus improving the fatigue resistance of the workpiece and increasing The adhesion between it and the coating prolongs the durability of the coating film, and is also conducive to the leveling and decoration of the coating, removes impurities, variegated colors, and oxide layers on the surface, and at the same time roughens the surface of the medium to eliminate workpiece residues Stress and increase the surface hardness of the substrate.
Application range
Applicable product materials: all kinds of rubber (including silica gel), injection molded parts, magnesium alloy, aluminum alloy, zinc alloy and other materials.
Applicable product industry: 3C industries such as aerospace, automobile, construction, electronics, lighting, furniture, kitchen and bathroom, computer, communication, and home appliances.
The sandblasting machine has a wide range of applications, no matter what kind of workpiece, ranging from ship hulls, steel structures, and containers, to watch cases, buttons, injection needles, etc.; in addition to the existing standard sandblasting machines in the production industry, it also undertakes The development and manufacture of various special-shaped sandblasting equipment can be customized according to customer workpieces.
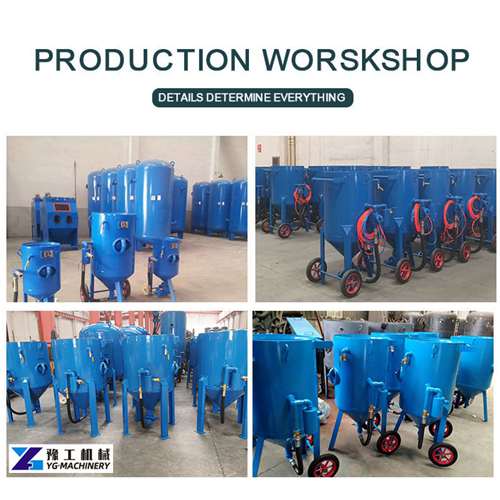
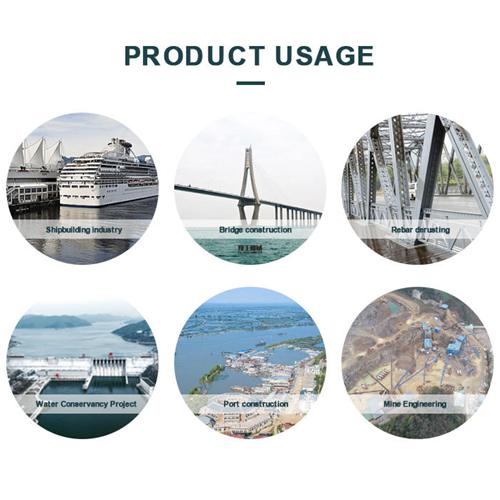
Types of Sandblasters
Fully automatic conveying sandblasting machine, turntable automatic sandblasting machine, deburring sandblasting machine, double gun basket automatic sandblasting machine, mobile rust removal sandblasting machine, liquid sandblasting machine, water type sandblasting machine, small manual Sandblasting machine, pass-through shot blasting machine, crawler shot blasting machine, hook shot blasting machine, sandblasting gun, nozzle, sandblasting machine gloves and sandblasting abrasives.
Suction sandblasting machine
General composition
A complete sand suction machine generally consists of six systems, namely structural system, medium power system, piping system, dust removal system, control system and auxiliary system.
Working principle
Suction blasters are powered by compressed air. Through the negative pressure formed by the high-speed movement of compressed air in the spray gun, the abrasive is sucked into the spray gun through the sand delivery pipe, and ejected at high speed through the nozzle. Abrasives ejected at high speed impact the surface of the workpiece to achieve the purpose of processing. In a suction blasting machine, the compressed air not only creates the suction that draws the abrasive into the gun, but also the acceleration that ejects the abrasive from the gun.
Press into the sandblasting machine
A complete press in a sandblasting machine generally consists of six systems, namely a structural system, medium power system, piping system, dust removal system, control system, and auxiliary system.
Working principle
The press of the sandblasting machine is driven by compressed air. Through the working pressure established by the compressed air in the abrasive tank, the abrasive is pressed into the spray gun through the sand delivery pipe and sprayed out at high speed through the nozzle. The high-speed spray abrasive impacts the surface of the workpiece to achieve the purpose of processing. In the press of the sandblasting machine, the compressed air not only creates the pressure of the abrasive entering the spray gun but also produces the acceleration power of the abrasive sprayed from the spray gun.
Wet sandblasting machine
The working state of the abrasive is dry and anhydrous, which is called a dry sandblasting machine. The working state of the abrasive is wet water, which is called a wet sandblasting machine. Compared with the dry sandblasting machine, the characteristic of the wet sandblasting machine is to control dust pollution during the sandblasting process and improve the working environment of the sandblasting operation. In addition, the wet sandblasting machine is a suction type, not a press-in type, because the abrasive tank is made of carbon steel, which is not resistant to water and sand washing and is easy to rust.
General composition
A complete wet blasting machine generally consists of five systems, namely the structural system, medium power system, piping system, control system, and auxiliary system.
Working principle
The wet sandblasting machine is powered by a sand pump to supply grinding fluid. The well-stirred grinding fluid (a mixture of abrasive and water) is delivered to the spray gun through a sand pump. Under the acceleration of compressed air, the grinding fluid is sprayed out through the nozzle at high speed. The high-speed sprayed grinding fluid scours the surface of the workpiece to achieve the purpose of processing. In a wet sandblasting machine, the sand pump provides pressure for the slurry to enter the spray gun. The compressed air provides acceleration power for the abrasive slurry to be ejected from the spray gun.
Conclusion
In short, different types of sandblasters should be selected according to the type of workpiece. For steel structural parts, in order to improve production efficiency, of course, the press in the sandblasting machine is a good choice. For the surface finish of handicrafts such as glass or aluminum alloy parts, it is necessary to choose a suction sandblasting machine. Because it does not require much processing force. For dust-free workshops, wet sandblasting machines are the main choice. But good workpieces are aluminum alloy or stainless steel parts that can be processed in water. For other materials, even if the workpiece dries quickly, water stains will occur and affect the coating quality.