Setting up a concrete mixing plant is a critical process in the construction industry, enabling the efficient production of high-quality concrete. This guide provides a step-by-step overview of establishing a concrete mixing plant, covering essential phases from preliminary planning to operational setup.
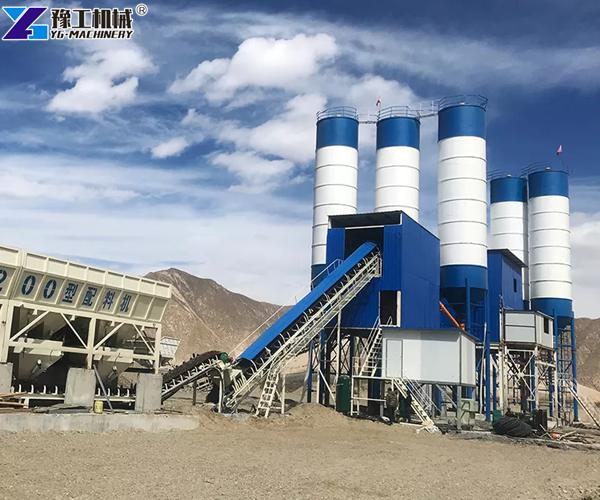
Essential Equipment Needed for a Concrete Mixing Plant
A concrete batching plant is an essential facility for the production of concrete, a material crucial for construction projects of all sizes. To ensure the effective and efficient manufacture of high-quality concrete, a variety of equipment is necessary. At the heart of the operation lies the concrete mixer, which is responsible for combining the raw materials—cement, aggregates, water, and additives—into a uniform mixture. Whether a stationary or mobile mixer is used, the performance of this equipment significantly impacts the consistency and quality of the final product.
In addition to the mixer, a concrete mixing plant requires a reliable aggregate storage system. This system is typically composed of bins or hoppers that store different types of aggregates, such as sand, gravel, and crushed stone. A well-designed storage solution allows for easy access and efficient handling of materials, reducing downtime and facilitating a smooth workflow. Furthermore, conveyors or bucket elevators are necessary for transporting aggregates from storage to the mixer, ensuring that the mixing process is both swift and seamless.
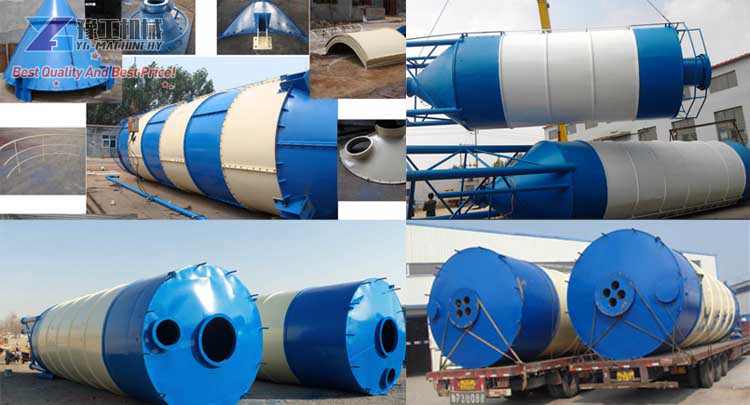
Water and additive dosing systems are also critical components of a concrete mixing plant. Accurate measurement of water is essential for achieving the right consistency and strength in the final concrete mix. Devices like water flow meters and additive dispensers enable precise control over the mix’s components, promoting not only quality but also compliance with specific project requirements. With the right equipment in place, operators can optimize the production process, reducing waste and improving overall efficiency.
Finally, supplementary equipment such as control systems, scales, and batching systems plays a vital role in the operation of a concrete mixing plant. These systems monitor and manage the mixing process, ensuring that all components are blended in the correct proportions. By integrating advanced technology, operators can enhance precision and maintain robust quality control, allowing for consistent results that meet the demands of both small-scale and large-scale construction projects. In summary, the essential equipment needed for a concrete mixing plant serves to streamline production, maintain quality, and ultimately support the success of construction endeavors.
How to Properly Set Up a Concrete Mixing Plant
- Preliminary Project Research: Before starting the setup, it’s essential to conduct comprehensive research to grasp the project requirements, such as the amount of concrete needed and the specific mix designs. This foundational understanding will guide future decisions regarding equipment and site selection.
- Site Selection: Select a suitable location that complies with local regulations and offers easy access to essential raw materials like aggregates, water, and power sources. The site should also facilitate safe and efficient operations.
- Design and Construction: Create a detailed design for the plant layout, ensuring it includes all necessary components like mixers, silos, and conveyors. Build a solid foundation that can support the weight of the equipment and ensure proper drainage.
- Equipment Installation: Systematically install the various components of the batching plant according to the manufacturer’s instructions. This includes assembling mixers, conveyors, and storage bins while ensuring all connections are secure.
- Configuration and Calibration: After installation, set up the plant’s control systems to meet project specifications. This step involves entering material proportions and mix designs into the software that manages the batching process.
- Operational Procedures: Develop standard operating procedures for safely and efficiently starting up the plant. This includes a checklist for powering up equipment in the correct order to reduce risks and ensure optimal performance.
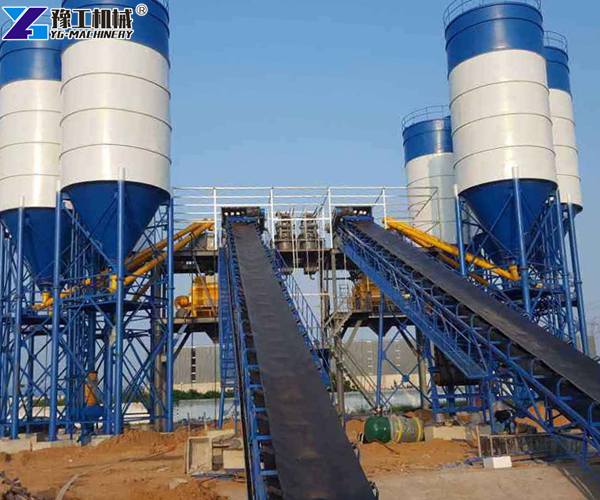
Maximizing Productivity in Your Concrete Mixing Plant
To begin with, one of the most important factors is to streamline the mixing process itself. This involves sizing up the equipment appropriately to match production demands. Investing in high-quality concrete mixers that offer quick batch cycles can significantly reduce downtime, allowing for a more consistent output. Regular maintenance and timely upgrades of equipment are also essential to prevent unexpected breakdowns that can halt production.
Another critical aspect is implementing effective inventory management strategies. Keeping a well-organized inventory of raw materials such as cement, aggregates, and additives ensures that production flows smoothly without disruptions. Utilizing a just-in-time inventory system can help minimize waste and reduce storage costs, while also ensuring that the materials needed for each batch are readily available. Training staff on inventory tracking technologies can further enhance this process, enabling better forecasting and resource allocation.
Efficiency can also be boosted by optimizing workflow processes within the concrete mixing plant. This involves assessing the layout of the plant and making adjustments to facilitate better movement of materials and personnel. Employing Lean principles can help identify wasteful practices, ensuring that every step of the mixing process adds value to the final product. Additionally, investing in automation technologies, such as conveyor systems and batching software, can significantly cut down on manual labor and improve consistency in production rates.
Finally, fostering a culture of continuous improvement among workers can lead to innovative solutions that enhance productivity. Encouraging team members to share their insights and experiences can uncover potential bottlenecks and inefficiencies in the concrete mixing plant. Providing training and development opportunities ensures that employees are equipped with the skills needed to adapt to new technologies and methodologies. By creating an environment focused on collaboration and open communication, concrete mixing plants can not only increase productivity but also elevate overall worker satisfaction and engagement.