Jaw crushers and cone crushers are two of the most common types of stone crushers used in mining and construction. Both types of crushers use compressive force to break down rocks, but they have different advantages and disadvantages. Which is right for you? Read this article.
Jaw Crusher vs. Cone Crusher
Cone crushers have a wide range of uses and high crusher efficiency. Cone crushers are divided into three types: coarse crushing, medium crushing and fine crushing according to the scope of use.
- Standard type cone crusher – medium crushing equipment
- Fine crushing equipment – short-head cone crusher
However, the coarse crushing equipment either uses a cone crusher or a jaw crusher. In order to correctly select and rationally use coarse crushing equipment, they are briefly analyzed and compared as follows.
Main advantages of cone crusher (compared to jaw crusher):
- The depth of the crushing cavity is large. Continuous work. High production capacity. The unit power consumption is low. Compared with the jaw crusher with the same width as the ore feeding opening, its production capacity is more than double that of the latter, while the power consumption per ton of ore is 0.5-1.2 times lower than that of the jaw crusher;
- The work is relatively stable, the vibration is light, and the basic weight of the machine equipment is small. The basic weight of the cone crusher is usually 2-3 times the weight of the machine equipment, while the basic weight of the jaw crusher is 5-10 times the weight of the machine itself;
- It can be packed with ore. The large cone crusher can directly feed raw ore without the need for additional ore bins and ore feeders. The jaw crusher cannot be crowded with ore feeders, and the ore feeders are required to be uniform, so an additional ore bin (or ore feeder funnel) and ore feeder are required. When the ore size is greater than 400 mm, expensive heavy-duty plate crushers need to be installed. To the mining machine;
- The cone crusher is easy to start, unlike the jaw crusher which requires the use of auxiliary tools to rotate the heavy flywheel before starting (the exception is the segmented start-up jaw crusher);
- The cone crusher produces less flaky products than the jaw crusher.
Disadvantages of cone crushers
However, cone crushers also have the following disadvantages:
1. The rotating body is higher, generally 2-3 times higher than the jaw crusher, so the construction cost of the plant is relatively high;
2. The weight of the machine is large. It is 1.7-2 times heavier than a jaw crusher with the same size of the ore opening, so the investment cost is higher;
3. It is not suitable for crushing wet and sticky ores;
4. Installation and maintenance are complicated, and maintenance is inconvenient.
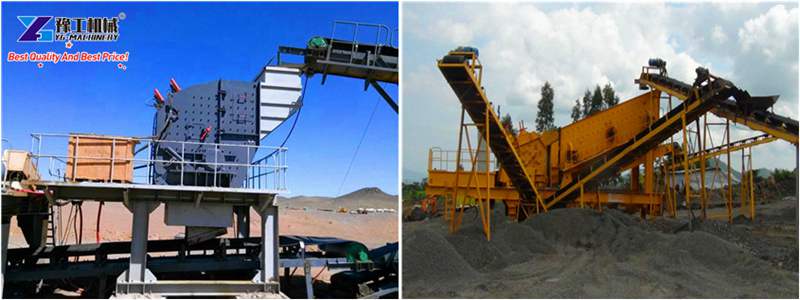
Which type of crusher is right for you?
The best type of crusher for you will depend on your specific needs. When selecting coarse crushing equipment in the design, the nature of the ore, the particle size requirements of the product, the scale of the dressing plant and the configuration conditions of the equipment should also be considered.
If you need a crusher for primary crushing, a jaw crusher is a good option. If you need a crusher for secondary or tertiary crushing, a cone crusher is a good option.
Characteristic | Jaw Crusher | Cone Crusher |
---|---|---|
Reduction ratio | 3:1 to 6:1 | 4:1 to 8:1 |
Efficiency | Moderate | High |
Operating costs | Low | Moderate |
Maintenance costs | Low | Moderate |
Durability | High | High |
Applications | Primary crushing | Secondary and tertiary crushing |
In conclusion
It is recommended that when the ore being processed is flake or strip-shaped hard ore, two or even more jaw crushers are needed to meet production requirements. But, when a cone crusher can be used instead, the cone crusher should be preferred.
This solution is more advantageous especially when the coarse crushing plant is located on a slope. When crushing wet and sticky ores, or in small and medium-sized processing plants with smaller production scale, jaw crushers should be used. As for underground crushing, jaw crushers are usually used.